[Congnghehcv] Tiến Trình Công Nghệ Gia Công Bánh Răng
Link tải file bài viết
Chuẩn định vị khi gia công
Tuỳ theo kết cấu, độ chính xác, sản lượng ta có:
- Chuẩn tinh chính thống nhất thường là lỗ và mặt đầu, (yêu cầu phải đảm bảo vuông góc giữa mặt đầu và tâm lỗ, nên lỗ và mặt đầu phải được gia công trong một lần gá).
- Trong sản xuất nhỏ ở nguyên công đầu thường dùng mặt đầu và mặt ngoài làm chuẩn thô.
- Sau nhiệt luyện nếu mài lỗ nên định vị vào vòng lăn.
- Với bánh răng liền trục: chuẩn định vị là mặt đầu, cổ trục hoặc hai lỗ tâm.
Tiến trình công nghệ
Ở tiến trình này, người ta xác định tiến trình công nghệ bao gồm các bước cơ bản. Ở đây có gia công thô; gia công tinh; gia công mặt ngoài rồi mới Phay ren, then hoa, lỗ và cắt ren. Tiến trình Công Nghệ Gia Công Bánh Răng bao gồm:
- Gia công thô lỗ.
- Gia công tinh lỗ.
- Gia công thô mặt ngoài.
- Gia công tinh mặt ngoài.
- Phay then, then hoa, khoan lỗ, cắt ren…
Trong sản xuất nhỏ thì gia công trên máy tiện, lỗ được doa.
Trong sản xuất lớn: Chuốt lỗ sau khi khoan hoặc khoét rồi gia công các mặt còn lại trên máy bán tự động hoặc trên dây truyền tự động.
Bánh răng có D > 500 mm thường được gia công trên máy tiện đứng.
Các phương pháp cắt răng
a. Phương pháp định hình
- Prôfin dao phù hợp với profin bánh răng. Thường dùng dao phay đĩa hoặc ngón môđun.

Hình 5.2. Cắt răng trụ bằng dao phay môđun
- Sau khi phay xong một rãnh phôi được phân độ một góc
=360
/z.
- Phay trên máy phay vạn năng có dụng cụ chia độ.
- Khi gia công bánh răng thẳng trục dao và chi tiết song song còn khi gia công bánh răng nghiêng trục dao và chi tiết nghiêng một góc bằng góc nghiêng ở vòng chia của bánh răng.
- Có thể gia công bánh răng trụ (thẳng, nghiêng) hoặc chữ V (bằng hai lần hoặc một lần trên máy bán tự động chuyên dùng).
- Dạng trong sản xuất nhỏ, sửa chữa hoặc bánh răng có môđun lớn.
- Độ chính xác thấp (cấp 7
8) do nhiều nguyên nhân.
- Làm việc ở vận tốc thấp V < 5m/phút.
- Dao được sản xuất theo bộ: 8 ; 15 ; 26 con.
- Chọn số hiệu dao: Với bánh răng thẳng
Bảng 5.3. Bộ dao phay với 8 dao
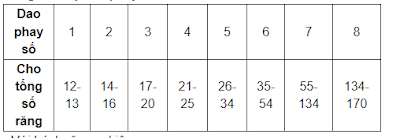
- Với bánh răng nghiêng:
- Dùng gia công phá những bánh răng có môđun lớn trong sản xuất lớn.

Hình 5.4. Cắt răng thô bằng dao phay đĩa
Dùng dao phay góc hình 5.4.a.
Hoặc dùng dao phay đĩa chuyên dùng hình 5.4.b.
- Có thể dùng xọc định hình năng suất thấp nên ít dùng.
- Dùng chuốt định hình (một rãnh hoặc nhiều rãnh cùng lúc) cho năng suất và độ chính xác cao. Nhưng lực lớn, dao khó chế tạo. Chỉ nên dùng cho sản xuất lớn và bánh răng môđun lớn không qua nhiệt luyện hoặc mài.

Hình 5.2. Sơ đồ chuốt răng
b. Phương pháp bao hình
Profin bánh răng được tạo ra là hình bao những vị trí liên tiếp của lưỡi cắt của dao profin dao không cần giống profin chi tiết gia công
- Phay lăn răng
- Năng suất cao, độ chính xác tốt - nên dùng khá phổ biến.
- Gia công được răng bánh răng và bánh vít.
- Tiến hành trên máy chuyên dùng.
- Phay liên tục, chia độ tự động.
- Dao có dạng trục vít vô tâm mà prôfin ở mặt pháp tuyến là thanh răng cơ bản.
- Cấu tạo dao phay lăn

Hình 5.6. Dao phay lăn răng
Khi phay lăn răng bánh răng thẳng:
+ Trục dao và chi tiết chéo nhau một góc bằng góc nâng của dao ở vòng chia
Có thể phay thuận hoặc phay nghịch, nhưng chủ yếu dùng phay nghịch.

Hình 5.7. Sơ đồ cắt khi phay lăn răng
a. phay thuận; b. phay nghịch.
- Dao phay có đường kính càng lớn thì hiệu quả cắt càng lớn, chất lượng bề mặt và độ chính xác cao nhưng năng suất không cao.
- Có thể tiến dao hướng trục, hướng kính hoặc phối hợp.

Hình 5.8. Các phương pháp tiến dao
a. tiến dao hướng trục; b. tiến dao hướng kính và hướng trục
- Khi phay răng nghiêng: trục dao và chi tiết chéo nhau một góc:

Hình 5.1. Sơ đồ gá dao khi phay răng nghiêng
a. dao xoắn phải; b. bánh răng nghiêng phải; c. bánh răng nghiêng trái.
- Khi phay răng nghiêng có thêm chuyển động vi sai lượng chạy dao thêm hoặc bớt một lượng 
.
- Zc: Số bánh răng cần gia công.
-
=
.
-
góc gá trục dao.
-
: góc nghiêng trên vòng chia của bánh răng gia công.
- Vận tốc cắt thường V = 15 - 30m/p. Dao hợp kim cứng V = 60 -70m/p.
- Lương chạy dao dọc có ảnh hưởng lớn đến độ nhấp nhô bề mặt RZ.
- Để điều chỉnh máy thuận tiện người ta thường lấy lượng chạy dao dọc trong một phút.
Để tăng năng suất
+ Có thể dùng dao phay có hai, ba đầu mối nhưng khi đó chất lượng gia công giảm so với dao một đầu mối.
+ Dùng dao đặc biệt như dao Xiđôrencô hoặc dao Philatôp khi đó sẽ tăng được lượng chạy dao.
+ Có thể gá nhiều chi tiết để gia công cùng một lúc.
- Có thể phay thô, bán tinh, phay tinh bằng các dao phay lăn tương ứng.
Tuy nhiên phay lăn cũng có nhược điểm:
+ Dao phức tạp khó chế tạo
+ Khoảng thoát dao phảI lớn
- Xọc răng
Dùng dao xọc răng hình hình đĩa hoặc hình cốc
- Có thể gia công được cả bánh răng tầng, bậc, bánh răng có vai, bánh răng trong.
- Chuyển động tạo hình

Hình 5.3. Sơ đồ xọc răng
- Khi gia công không thể cắt ngay một lúc hết chiều sâu rãnh răng bánh răng mà phải từ từ tiến dao hướng kính nên cần lưu ý chuyển động ăn dao.
- Tuỳ theo mô đun của bánh răng mà có thể ăn dao 1 lần, 2 lần hoặc 3 lần.
- Có thể dùng dao xọc ngoài để gia công bánh răng trong:
- Máy xọc không có xích vi sai mà nó được thực hiện nhờ có bạc dẫn khi đó dao xọc vừa có chuyển động quay vừa có chuyển động xoắn.

1. bạc dẫn; 2. bánh răng; 3. rãnh dẫn nghiêng.
Hình 5.4. Sơ đồ xọc bánh răng nghiêng
Thời gian máy: T
=
+
. I
h- chiều cao răng ( mm )
m- mô đun bánh răng
z- số răng của bánh răng gia công.
Các biện pháp giảm thời gian, tăng năng suất.

Hình 5.5. Các phương pháp tăng năng suất khi xọc răng
a. cắt thô và cắt tinh cùng một lúc; b. gia công bánh răng bậc;
c. gia công nhiều bánh răng cùng lúc; d. xọc và phay bánh răng bậc;
e. xọc răng bằng nhiều lưỡi cắt.
- Vê, vát đầu răng
- Cho bánh răng cần di trượt.
- Có thể dũa bằng tay hoặc thực hiện trên máy chuyên dùng bằng dao phay ngón định hình.
- Các dạng vê và vát đầu răng: Dao chuyển động quay và chuyển động tịnh tiến đi lại để vê hai đầu răng kề nhau.
c. Gia công tinh bánh răng trụ
Có hai cách có phoi và không phoi (chạy rà)
- Chạy rà
- Cho bánh răng gia công ăn khớp với một hoặc ba bánh răng mẫu được tôi cứng và có độ chính xác cao.
- Dùng gia công bánh răng không nhiệt luyện, cho quay hai chiều với:
n = 1 đến 25 v/p
áp lực P = 5 đến 10 atm
- Khi chạy rà có thể bôi dầu

Hình 5.6. Sơ đồ chạy rà bánh răng trụ với ba bánh răng mẫu
1. bánh răng gia công; 2, 3. các bánh răng mẫu.
- Cà răng
- Gia công bánh răng chưa hoặc không nhiệt luyện.
- Trước khi cà bánh răng phải chế tạo khá chính xác. Sau khi cà độ chính xác được nâng lên từ 1 đến 2 cấp.
- Lượng dư cà nhỏ (0,1 - 0,25 mm cho một răng).
- Gia công bánh răng thẳng, nghiêng,trong hoặc ngoài.
- Dao cà lăn và trượt trên mặt răng lấy đi lớp phoi 0,001 - 0,002.

Hình 5.7. Sơ đồ cà răng (a) và cấu tạo của dao cà (b)
1. dao cà; 2. bánh răng gia công.
- Cà răng có khả sửa sai số hình dáng, bước răng, nâng cao độ nhẵn (Ra = 0,63
0,16).
- Có thể gia công được bánh răng có đường kính đến 1200mm môđun đến 12
- Có thể cà bằng dao hình đĩa hoặc thanh răng (ít dùng hơn).

Hình 5.5. Cà răng bằng dao cà dạng thanh răng
- Chỉ có dao nhận chuyển động còn bánh răng quay tự do.
- Trục dao cà và bánh răng gia công chéo nhau một góc
= 50 – 150
- Tuỳ theo phương pháp chạy dao mà có các phương pháp cà:
+ Cà song song: Chiều chạy dao song song với tâm bánh răng. Bánh răng gia công dịch chuyển song song với trục của nó. Dùng để gia công bánh răng thẳng và nghiêng.
+ Cà chéo: Chiều chạy dao chéo với tâm bánh răng, giảm được hành trình nên năng xuất của phương pháp này tăng. Nên chọn chiều rộng của bánh cà nhỏ hơn 63 mm là có lợi nhất.
+ Cà tiếp tuyến: Chiều chạy dao vuông góc với tâm bánh răng, khoảng cách giữa trục dao và trục chi tiết không thay đổi. Quá trình cắt được hoàn thành sau một hành trình kép của bàn máy. Dùng để chế tạo bánh răng có vành hẹp, vành kín.
+ Cà vuông góc: Bánh răng gia công dịch chuyển theo hướng vuông góc với trục dao. Quá trình cắt được hoàn thành sau một hành trình kép của bàn máy.

Hình 5.16. Các sơ đồ cà răng
a. cà song song; b. cà chộo; c. cà tiếp tuyến; d. cà vuụng gúc;
1. bánh răng gia công; 2. dao cà; C. điểm cắt nhau của các đường tâm dao và bánh răng gia công; A-A. đường tâm của trục dao; B-B. đường tâm của trục bánh răng gia công.
Lượng dư để cà từ 0,25
0,1mm
- Mài răng
- Gia công tinh bánh răng trước hoặc sau nhiệt luyện đạt: Cấp chính xác từ cấp 4
6, Ra = 1,25
0,32, máy mài răng phức tạp, năng suất thấp, giá thành cao nên chỉ dùng trong sản xuất lớn.
Có hai phương pháp:
- Phương pháp định hình
+ Mài một hoặc hai bên răng bằng một hoặc hai đá.
+ Mài hai mặt bên của một răng bằng một đá thì profin đá phụ thuộc vào: môđun, số răng và góc áp lực nên độ chính xác thấp.

Hình 5.17. Sơ đồ mài răng bằng đá mài định hình
a. mài định Hình một mặt bên của răng; b. mài định Hình hai mặt bên của răng bằng một đá mài; c. mài định Hình hai mặt bên của răng băng hai đá mài cùng một lúc.
+ Mài hai mặt bên bằng hai đá cho độ chính xác cao hơn,
+ Hình dáng đá ban đầu và sự mòn không đều của đá sẽ trực tiếp gây gây sai số.
+ Đá cần được sửa theo dưỡng hoặc có bộ phận sửa đá tự động.
+ Vận tốc khi mài V = 30
35m/s, vận tốc tiến của đá S = 6
16m/f, lượng dư mài khoảng 0,2mm chia thành 3
4 bước.
+ Có thể gia công bánh răng ngoài và trong.
+ Cần có nhiều dưỡng chép hình, đĩa chia độ, điều chỉnh máy phức tạp nên độ chính xác và năng suất không cao.
Mài bao hình.
Mài bao hình cho độ chính xác và năng xuất cao hơn mài định hình. Dựa vào sự ăn khớp của thanh răng và bánh răng có cùng môđun và góc ăn khớp. Các loại đá thường dùng là:
Mặt côn của một hoặc hai đá đĩa, đá và răng tiếp xúc điểm.

Hình 5.18. Mài răng bằng đá mài có prôfin hình thang của thanh răng
a. mài bằng một đá có prôfin hình thang của thanh răng.
b. mài bằng hai đá dạng đĩa được đặt nghiêng một góc sao cho hai mặt côn của đá tạo thành prôfin hình thang.
1. đá mài; 2. thanh răng tưởng tượng; 3. bánh răng gia công; 4. chuyển động tịnh tiến lắc lư của bánh răng; 2. chuyển động tịnh tiến đi lại dọc trục bánh răng;
6. chuyển động lắc lư của bánh răng.
Mặt đầu của hai đá đĩa trục đá và bánh răng có thể nghiêng một góc hoặc vuông góc, mặt đá và mặt răng tiếp xúc đường.

Hình 5.4. Mài răng bằng hai đá mài dạng đĩa được đặt nghiêng một góc bằng góc ăn khớp
1. đá mài; 2. thanh răng tưởng tượng; 3. bánh răng gia công; 4. chuyển động tịnh tiến lắc lư của bánh răng; 2. chuyển động tịnh tiến đi lại dọc trục bánh răng; 6. chuyển động lắc lư của bánh răng.

Hình 5.20. Mài răng bằng đá mài dạng đĩa có trục quay vuông góc với trục bánh răng gia công
1. đá mài; 2. bánh răng gia công; 3. chuyển động tịnh tiến lắc lư của bánh răng gia công; 4. chuyển động quay lắc lư của bánh răng gia công; 2. chuyển động tịnh tiến dọc trục bánh răng.
- Mài bằng đá trục vít
+ Năng suất cao vì gia công liên tục trên một số răng.
+ Đá mài có dạng trục vít một hoặc hai mối. Với đường kính bằng 300
400mm.
+ Vận tốc cắt khi Mài bằng đá trục vít (vận tốc đá quay) cỡ 22
32 m/s.
+ Đạt cấp chính xác 4
5 ; Ra = 1,25
0,16.
+ Bánh răng M < = 1 mài một lần nếu M > 1 thì mài hai lần.
+ Sửa đá lâu, phức tạp, nhiệt thoát kém.

Hình 5.21. Mài răng bằng đá mài trục vít
I. chuyển động quay của đá; II. chuyển động ăn dao hướng kính của đá; III. chuyển động quay của bánh răng gia công; IV. chuyển động tịnh tiến dọc trục bánh răng gia công của đá.
- Mài nghiền
- Nâng cao độ nhẵn, độ nhám sau khi nghiền có thể đạt Ra = 0,63
0,32, nhưng năng suất thấp.
- Có thể hiệu chỉnh sai số về dạng răng, bước và độ đảo vòng lăn (nhưng chỉ một phần nhỏ mà thôi).
- Có hai phương pháp nghiền: trục song song và trục nghiêng:
+ Nghiền trục song song: Bánh răng gia công chủ động và có chuyển động quay hai chiều và chuyển động dọc trục
+ Nghiền trục nghiêng: Năng suất và chất lượng cao hơn

Hình 5.22. Sơ đồ mài nghiền bánh răng
1. bánh răng gia công; 2, 3. bánh nghiền.
- Có hai biện pháp mài nghiền.
+ Có khe hở
+ Không có khe hở: hai bên sườn răng được mài đồng thời.

Hình 5.23. Các biện pháp nghiền
a. nghiền có khe hở; b. nghiền không có khe hở; 1. bánh nghiền;
2. bánh răng gia công.
- Mài khôn
- Sửa vết lồi lõm, nhấp nhô, sửa phần nào sai số hình dáng, khuyết tật do nhiệt luyện v.v,…
- Độ nhẵn Ra = 1,25
0,32.
- Bánh răng dụng cụ làm từ vật liệu nhám, hoặc vành ngoài nhám như: cacbit silic, cácbít Bo, kim cương nhân tạo…
- Trục dụng cụ và chi tiết phải chéo nhau. Nguyên lý làm việc như cà răng.
- Có hai biện pháp:
+ Mài cà có khe hở: sửa chữa những vết lõm, giảm độ nhám, nhưng sai số hình dáng răng sửa được ít.
+ Mài cà không có khe hở: sửa được sai số hình dáng.
Lượng dư nhỏ 0,025
0,05 phải dùng dung dịch trơn nguội
Thích hợp cho bánh răng có M = 2
6
d. Gia công bánh răng côn
Gia công bánh răng côn nói chung một cách chính xác thuộc loại khó gia công.
Phân loại bánh răng côn

Hình 5.24 Các loại bánh răng côn
a. răng thẳng; b. răng nghiêng; c. răng cong.

Hình 5.22. Các dạng chiều cao răng của bánh răng côn. (Hình 17.38 ).
a. chiều cao răng đều; b. chiều cao răng thay đổi.
- Gia công bánh răng côn thẳng
* Phương pháp định hình
- Phay định hình
+ Dùng dao phay đĩa, phay ngón có đầu chia độ
+ Góc quay của đầu chia độ bằng góc chân răng bánh răng
+ Cắt răng theo ba bước góc quay Tan
=
; trong đó: b
bề rộng rãnh răng ở đầu lớn; b
- bề rộng rãnh răng ở đầu nhỏ; l- chiều dài của răng.
+ Thường dùng cắt bánh răng mô đun lớn độ chính xác thấp.

Hình 5.26. Phay bánh răng côn bằng dao phay đĩa định hình
a. gá chi tiết gia công trên trục gá; b. sơ đồ phay rãnh răng.
- Bào theo dưỡng
+ Dùng gia công bánh răng có đường kính lớn và mô đun lớn
+ Răng của tất cả các bánh răng có cùng số răng sẽ có thông số hình học giống nhau.

Hình 5.27. Sơ đồ bào răng côn
a. sơ đồ dưỡng bào răng côn; b. sơ đồ động của bàn xe dao bào răng côn trên bàn máy OerlikonK4a; 1. bánh răng gia công; 2. bộ phận dẫn hướng; 2
; 2
; 2
. các dưỡng chép hình; 3. các dao; 4. bàn xe dao; 2. cơ cấu cam; 6. đối trọng.
* Phương pháp bao hình
- Răng được tạo nên bởi sự lăn của côn chia bánh răng gia công theo mặt phẳng chia của bánh dẹt sinh tưởng tượng (là bánh răng côn có góc côn đỉnh bằng 1800).
- Dụng cụ là một hoặc hai dao có lưỡi cắt thẳng (chính là răng của bánh dẹt sinh). Chuyển động khứ hồi theo hướng côn chia của bánh răng.
- Dụng cụ gá lên đầu dao và đầu dao thực hiện chuyển động ăn khớp với bánh răng gia công.
- Các phương pháp gia công:
+ Phay bằng hai dao đĩa Có năng suất cao.
Mặt bên dao phay có dạng răng của thanh răng.
Nguyên lý làm việc và các chuyển động như sau: Trục chính của dao đặt trên đầu của bàn trượt và quay với tốc độ nd kết hợp với chi tiết quay nc tạo ra chuyển động bao hình.
Khi chiều rộng vành răng nhỏ thì dao không cần chuyển động chạy dao S, nếu > 20mm thì phải có chạy dao dọc S
Khi phay xong một rãnh thì dao chuyển về vị trí ban đầu còn chi tiết tự động phân độ một góc răng.
+ Bào bao hình là bào bằng một hoặc hai dao có dạng hình thang gá trên rãnh đầu dao quay, dao chuyển động khứ hồi trùng với đường côn chân răng đồng thời quay cùng với đầu dao xung quanh trục của nó với vận tốc nd ăn khớp với chi tiết quay với vận tốc nc tạo ra xích bao hình.
Bao hình từng răng, xong một răng lại phân độ để gia công tiếp (phân độ vừa liên tục vừa gián đoạn).

Hình 5.28. Bào bao hình bánh răng côn
1. trục chính; 2. bánh răng gia công; 3. đầu dao
+ Mài bao hình
Dùng một hoặc hai đá đĩa phẳng hoặc côn.
Đá mài đặt vào con trượt trên mâm lắc.
Mâm lắc có chuyển động thích ứng với bánh răng tạo ra xích bao hình.
Mài từng răng, trong quá trình mài bánh răng phân độ liên tục để gia công.
Lượng dư mài từ 0,07
0,12mm.

Hình 5.21. Sơ đồ mài bánh răng côn thẳng
1. đá mài; 2. bánh răng gia công; 3. mâm lắc.
- Gia công bánh răng côn cong côn xoắn
+ Khả năng truyền động lớn, êm, ít ồn, hệ số trùng khớp cao, tỷ số truyền lớn mà không gian nhỏ gọn.
+ Lực chiều trục lớn thiết bị gia công phức tạp, đắt tiền.
Căn cứ vào hướng răng ta có 3 loại:
1- Răng cung tròn – thuộc hệ Gleanson.
2- Răng cung Epixicloit – Mam – mano
3- Răng cung thân khai – thuộc hệ Klin – Gelnberg.
Kiểm tra bánh răng
Sau khi chế tạo bánh răng, chúng ta cần phải thực hiện thao tác kiểm tra các thông số của bánh răng, kể cả động học và hình dạng kích thước. Bao gồm những những nội dung sau:
+ Độ chính xác động học:
Kiểm tra khi có yêu cầu truyền chuyển động chính xác.
Sai số động học (sai số góc quay của bánh răng sau một vòng quay).
Sai số tích luỹ bước vòng.

Hình 5.36. Kiểm tra sai số tích lũy bước vòng
1. bánh răng cần kiểm tra; 2. chốt định vị; 3. đĩa chia; 4. đầu đo; 2. đầu đo của đồng hồ so.
Độ đảo vòng chia.

Hình 5.37. Kiểm tra độ đảo vòng chia
Sai lệch khoảng pháp tuyến chung.

Hình 5.38. Kiểm tra sai lệch pháp tuyến chung
Sai lệch khoảng cách tâm khi bánh răng quay một vòng.
+ Độ ổn định khi làm việc:
Kiểm tra khi làm việc ở tốc độ cao bao gồm các chỉ tiêu sau:
a- Sai số chu kỳ.
b- Sai lệch bước cơ sở.
c- Sai số bước vòng.

Hình 5.31. Sơ đồ kiểm tra bước vòng
Sai số prôfin.

Hình 5.40. Kiểm tra sai lệch prôfin sau khi gia công bánh răng
a. kiểm tra bằng máy; b. kiểm tra bằng dưỡng; 1. thước; 2. bánh răng kiểm tra; 3. đĩa; 4. đầu đo; 2. đồng hồ so; 6. đầu tỳ.
Sai lệch khoảng cách tâm khi bánh răng quay một răng.
+ Độ chính xác tiếp xúc, kiểm tra khi làm việc có tải trọng lớn gồm các chỉ tiêu:
a- Diện tích tiếp xúc
b- Sai lệch phương răng
+ Khe hở mặt bên kiểm tra khi bánh răng làm việc cả hai chiều